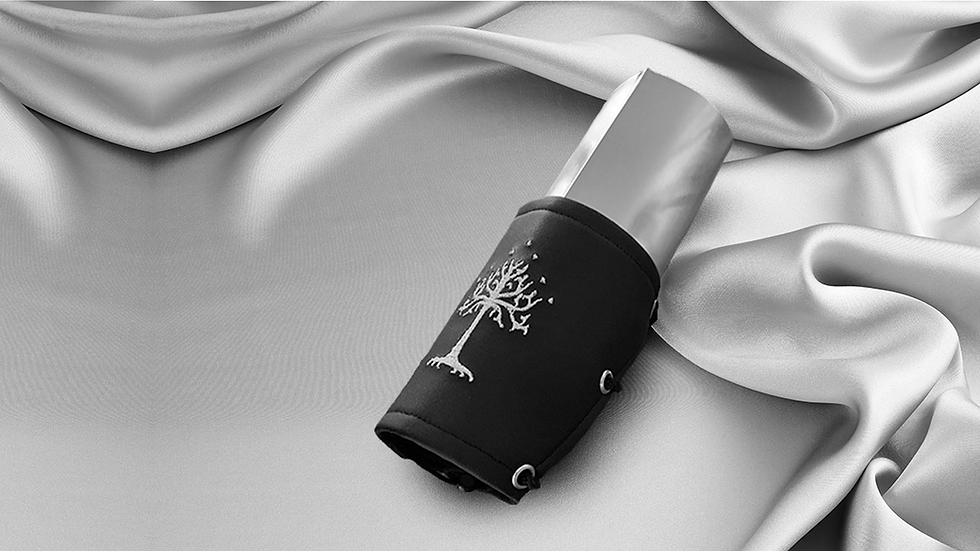
MONOLITH PROSTHETICS
Going From Universal To Personal
The physical product adaptation of my BFA senior thesis involving manufacturing.
From Universal to Personal
As simple as putting a case on a MacBook or phone. You don’t change the product; however, what changes is the appearance. We all want something that appeals to our personal interests. Not only does a case change your perception of your device, but it also attracts a certain audience. Every person has a personality, so why not display it. The overall goal is to apply these same philosophies to a prosthetic. People shouldn’t have to pay more for a personal connection. Let’s revolutionize a prosthetic simply by altering its appearance. Be proud of who you are.
Sketches
The purpose of the sketches featured above serve as blueprints to understanding the human anatomy and forearm configurations. As the exterior prosthesis was examined, the internal thickness was estimated and accounted for the purpose of product contour (how big can the exterior be and what are the constraints).
In creating something revolutionary, one must first understand the purpose of the prosthesis and find a way to create a symbiotic relationship with the desired product.
The picture on the left depicts a first iteration of the exterior prosthesis. The exterior is derived from the gauntlets of a Gondorian Citadel Guard from, The Lord of the Rings trilogy. The idea was create something fun and imaginative for a young child.
The drawing in the middle is the second iteration that challenges the realms of contour bending and angular cuts. Something that alludes to mediveal armor without any fantasy attributes.
The third and final sketch (bottom left) combines the worlds of industrialization and science fiction. Comprised of minimal aluminum cuts lined with leather. The demographic that this particular version is tailored towards are car and motorcycle enthusiasts.
Manufacturing/Production
The two main componets of the prosthetic exterior are leather and aluminum. The gaunlets are embroidered and outsourced to leather specialists. The aluminum is lasered cut to specific dimensions and contorted to specific angles. The interior is lined with black cotton cloth to match the leather. Only the child’s iteration features a wood cuppling of the Tree of Gondor (the tree featured on the gautlet). Both product iterations are adjustable to fit any prosthesis.
Once a dream, and now, a reality. Together, they form an identity. Each prosthesis exterior is showcased with its own aluminum stand. Minimal, but intricate. Inspired by Danish Design.
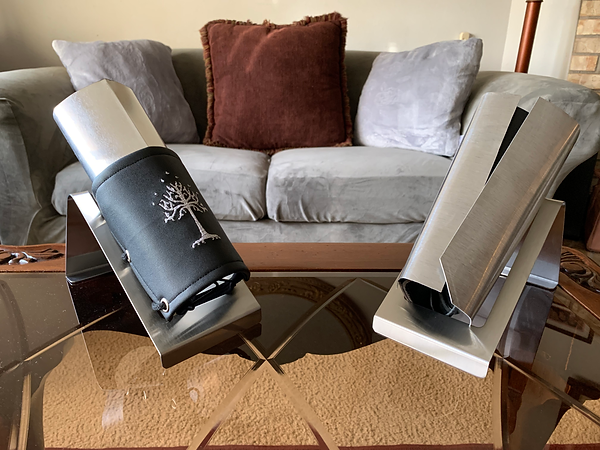
How's it used?
That's a great question! Unfortunately, I was never able to obtain an actual prosthetic or user within the projects timeframe. However, thanks to technology, I was able to render some touchpoints in photoshop. The vision maintained its authenticity.

Acrylic signage
An piece made out of clear acrylic was laser cut to the dimensions of 11 by 23 inches. A total of four holes were drilled in each corner to allow for wall placement or mounting. The reason behind the choice of material was to convey a corperate aesthetic and embody the wonders of industrial technology in the modern age.
Once the acrylic sign was cut, a heat treated vinyl grahic was placed in the center of the material. During the laser cutting process, the approximate depth for the logotype laser engraving was set to be less than 1/16 inches.
REDLINE ART GALLERY
For two weeks, I had the honor and privilege of having my BFA Thesis on display at the Redline Gallery. Everyone had the ability to witness the branding, process, and physical application all in one setting.
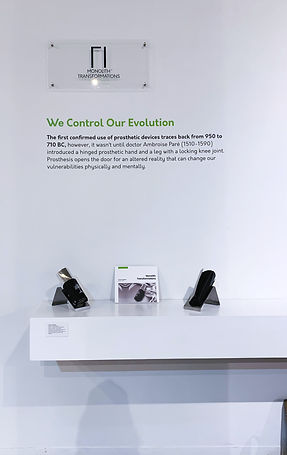